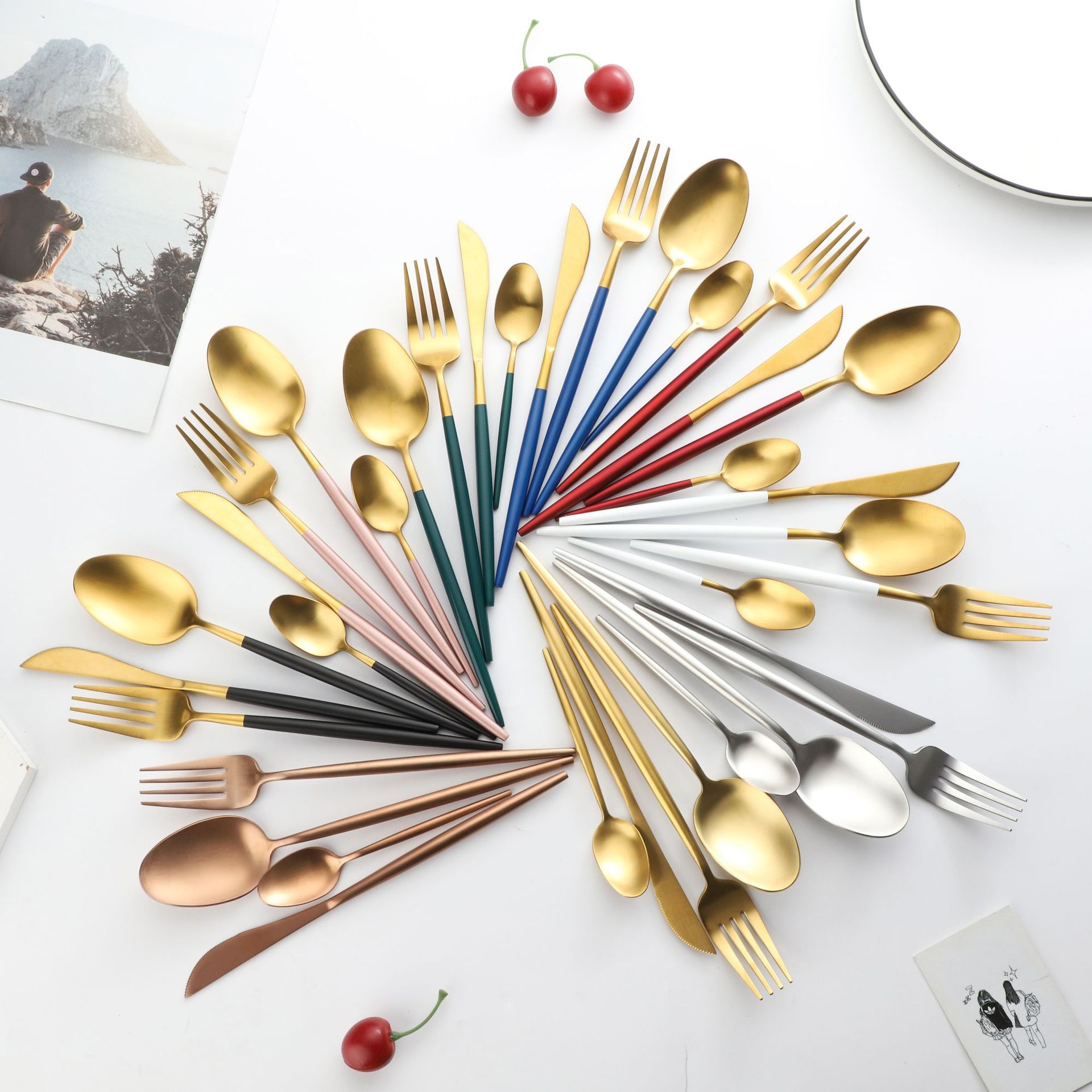
28 May
How is Plastic Cutlery Made?
How is Plastic Cutlery Made?Plastic cutl...
How is Plastic Cutlery Made?
Plastic cutlery is a popular choice in many homes, events, and businesses because of its convenience, durability, and cost-effectiveness. But have you ever wondered how plastic cutlery is made? In this article, we will walk you through the entire process of creating plastic spoons, forks, and knives, from raw materials to finished products.
1.1 The Beginning: Choosing Raw Materials
The first step in making plastic cutlery is selecting the raw materials. The primary material used is a type of plastic known as polypropylene (PP) or polystyrene (PS), which is chosen for its durability, resistance to heat, and flexibility. These plastics are both affordable and practical, making them ideal for mass production.
Additionally, factories like Homefelt ensure that only high-quality plastic is used, as the production process depends heavily on the plastic's properties. For example, Homefelt sources PP and PS in large quantities, ensuring that the plastic used for cutlery is both strong and lightweight.
1.2 Molding Process: Shaping the Cutlery
Once the raw materials are ready, the plastic is heated to a high temperature until it becomes molten. It is then injected into molds that are designed to create the shape of the cutlery items. This process is called injection molding. Molds for different types of plastic cutlery, such as spoons, forks, and knives, are used to ensure precision and consistency.
For example, Robert Welch spoons or similar high-quality spoons are produced with the utmost precision. Even in mass production, the importance of creating smooth edges and durable structures is emphasized.
1.3 Cooling and Solidifying
After the plastic has been injected into the molds, the next step is to cool and solidify the material. This cooling process helps the cutlery retain its shape and ensures that the plastic remains rigid and durable. This is a critical stage in the manufacturing process, as the product must be perfectly formed and ready for distribution.
During this step, the plastic cools and solidifies quickly, allowing for fast production cycles. The use of advanced technologies by factories like Homefelt helps maintain efficiency, ensuring that plastic cutlery is both high-quality and cost-effective.
1.4 Cutting and Finishing Touches
After cooling, the plastic cutlery is removed from the molds. However, the pieces still need to go through a finishing process. This is where any excess plastic is trimmed away, ensuring that the edges are smooth and free from defects.
At this stage, the cutlery is inspected for any imperfections. The final quality check includes ensuring that the cutlery is free from cracks, bubbles, or any other deformities. The result is a perfectly formed plastic knife, spoon, or fork, ready for distribution.
1.5 Packaging and Distribution
Once the plastic cutlery is finished, it is packaged in bulk or individual packs, depending on the requirements of retailers or consumers. Manufacturers like Homefelt ensure that the packaging is designed to protect the cutlery during transport, ensuring it arrives in perfect condition.
The cutlery is then ready for shipment to wholesalers or direct to businesses and consumers. This entire process is carefully planned to ensure that the plastic cutlery meets the highest standards of quality while being affordable for large-scale use.
Conclusion
Plastic cutlery is an essential part of many everyday activities, and understanding how it is made can help you appreciate the effort and technology involved in its production. From the raw materials to the final packaging, each step ensures that the cutlery is durable, practical, and cost-effective. Factories like Homefelt play an essential role in the production of high-quality plastic cutlery, making sure that products such as Robert Welch spoons and small kitchen knives are manufactured to perfection.